电木粉 (酚醛塑料粉)
类别: |
酚醛模塑料;酚醛注塑料 |
用途: |
PF2A1-131(R131)用于制造瓶盖和钮扣等日常生活用品。
PF2A2-131(D131)用于制造日用低压电器的绝缘结构件。
PF2A2-141(D141)、PF2A2-151(D151)用于制造低压电器的绝缘结构件及仪表壳等。
PF2A4-161(H161)本产品属于防湿热粉,用于制造湿热地区使用的低压电器和仪表的绝缘结构件。 |
包装: |
外为塑料编织袋,内衬聚乙烯薄膜袋的双层包装袋,或外为二合一纸袋,内衬聚乙烯薄膜袋的双层包装袋。 |
贮存: |
1、贮存在通风、干燥的仓库里,避免受潮、受热、受污和包装破损,温度不超过35℃ ,不得靠近火源、暖气或受阳光直射。
2、贮存期自生产之日起一年,超过贮存期应对质量指标逐项进行检验,如合格仍可使用。 |
产品规格: |
PF2A1-131[R131];PF2A2-131[D131];PF2A2-141[D141};
PF2A2-151[D151];PF2A4-161{H161} |
执行标准 :GB1404-1995
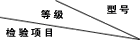
|
PF2A1-131[R131] |
PF2A2-131[D131]
PF2A2-141[D141}
PF2A2-151[D151] |
PF2A4-161{H161} |
体积系数≤ |
3.0 |
3.0 |
3.0 |
弯曲强度,mpa≥ |
70 |
70 |
70 |
冲击强度(缺口),KJ/m2≥ |
1.5 |
1.5 |
1.5 |
热变形温度,℃≥ |
140 |
140 |
140 |
绝缘电阻,Ω≥ |
- |
108 |
109 |
介电强度,(90℃),MV/m≥ |
- |
3.5 |
3.5 |
介质损耗因素,(1MHZ)≤ |
- |
0.1 |
0.1 |
吸水性,mg
≤ |
60 |
50 |
40 |
流动性 |
供需方商定 |
注:1、酚醛注塑料型号为酚醛模塑料型号后加"(J)"。
Type |
Classification |
Grade |
Features
and Applications |
General
Type(A) |
Household
(R) |
PF2A1-131 |
Suitable
for making handles or spare parts of daily
household articles. |
Electric
Appliance (D) |
PF2A2-131 |
Enhanced
electric leakage resistance, can be used to make
insulating structures for low voltage electric
appliances. |
PF2A2-141 |
With better
electric leakage resistance than D131, can be
used to make insulating structures for low
voltage electrical
appliances. |
PF2A2-151 |
With better
electric leakage resistance than D141, can be
used to make insulating structures for low
voltage electrical
appliances. |
Hot and
Humid (H) |
PF2A4-JS |
Similar to
PF2A2, but with good water
absorbency, suitable for making insulating
structure for low voltage electrical appliances
and meters in hot and humid
area. |
PD2A4-161 |
|
Special
Type |
Heat-resisting
(C) |
PF2C3-431 |
Heat-resisting,
suitable to make insulating structure of low
voltage, igniter or spark plug of mobiles and
motorcycles. |
Electrical
Type (E) |
PF2E6-985 |
Low medium
waste, improved absorbency, suitable to make
insulating parts for telecommunication and
radio, igniter of mobiles and
motorcycles. |
Wear-resisting
(S) |
PF2S1-5802 |
High
wearable property, used to make spare parts for
gas meters. |
Injection
Type (J) |
|
PF2A2-141J |
For
injection machine use only, technical properties
and application is similar to
D141. |
PF2A2-151J |
For
injection machine use only, technical properties
and application is similar to
D151 |
PF2A4-161J |
For
injection machine use only, technical properties
and application is similar to
D161 |
PF2C3-431J |
For
injection machine use only, technical properties
and application is similar to
C3-431 |
PF2E6-985J |
For
injection machine use only, technical properties
and application is similar to
E6-985 |
PF2S1-5802 |
For
injection machine use only, technical properties
and application is similar to
PF2S1-5802 |
Colored |
Series |
Models |
Black,
Violet, Red, Garnet brown, Green, Padauk
imitation and other basic colors. Special
requirements for other specifications, models or
colors are available against
smaples. |
Type |
Classification |
Grade |
Features and
Applications |
|
|
|
|
|
|
|
Technical
Parameters
Properties |
Parameters |
General
Type (A) |
Heat-resisting
(C) |
Electrical
Type (E) |
PF2A1 |
PF2A2 |
PF2A4 |
PF2C3 |
PF2E2 |
A
Testing Results of Moulding Compound
Samples |
Volumetric
Coefficient≤ |
3.0 |
3.0 |
3.0 |
4.0 |
3.0 |
Fluidity |
(1) |
B
Testing Results of Moulding Compound
samples |
Relatively
Density≤ |
1.45 |
1.45 |
1.45 |
2.0 |
1.85 |
Flexural
Strength, Mpa ≥ |
70 |
70 |
70 |
60 |
45 |
Impact
Strength |
with
gap,KJ/m2 (2 )≥ |
1.5 |
1.5 |
1.5 |
2.0 |
1.6 |
without
gap,KJ/m2 ≥ |
6.0 |
6.0 |
6.0 |
3.5 |
2.0 |
Hot
Distortion Temperature, ≥ |
140 |
140 |
140 |
155 |
140 |
Burning
Nature(Blazing Bar Method) |
- |
- |
- |
(3) |
- |
Insulation
Resistance, Ω ≥ |
- |
10
8 |
10
9 |
10
8 |
10
12 |
Dielectric
Strength (90 ), Mv/m ≥ |
- |
3.5 |
3.5 |
2.0 |
5.8 |
Medium
Waster factor (1MHz) ≤ |
- |
0.1 |
0.1 |
- |
0.020 |
Electric
leakage track resistance, V ≥ |
- |
- |
- |
175 |
- |
Shrinkage,
% ≤ |
- |
- |
- |
- |
- |
Water
Absorbency, mg ≤ |
60 |
50 |
40 |
40 |
15 |
|
|
|
|
|
|
|
|
|
|
|
|
|
Notes: 1) The testing method and index for fluidity are
determined by supplier and user. If there's no
special demand, our factory use rasching
method.
2)
Impact Strength is tested on the samples with
gap.
3)
The blazing bar leaves sample after 3 minutes,
there should not be any flame on sample within
30 seconds.
4)
For technical properties of injection materials,
please refer to relative index of different
types and models.
Moulding
Technicals
Model |
Pre-heating
Condition |
Moulding
Condition |
Temperature  |
Time
min |
Moulding Temperature  |
Pressure
MPa |
Product Thickness
(1mm)
Keeping Time
(Min.) |
H161
E2-985
C3-431
JS
D151 |
105±3 |
15 |
160±3 |
>30-40 |
1-1.5 |
D141
D131
R131 |
- |
- |
160±3 |
>30 |
0.6-1 |
|
|
|
|
|
|
|
|
|
|
|
Notes:
May not be pre-heated before moulding, but
should be degased one or twice. For those above
grade D151, it is suggested pre-heating is a
necessary procedure.
The
moulding condition can be adjusted according to
actual size, thickness, usage of products and
different moulding equipment. In principle, the
quality of finished products can not be
decreased.
Injection
setting
|
Pressure(MPa) |
Speed |
Time |
Teminal
Position |
Injection
Pressure 1 |
80-120 |
40-90 |
- |
65-45 |
Injection
Pressure 2 |
75-115 |
35-85 |
- |
45-35 |
Injection
Pressure 3 |
70-110 |
30-80 |
- |
25-25 |
Injection
Pressure 4 |
70-105 |
25-75 |
20 |
5-10 |
Keeping
Pressure 1 |
80-90 |
30-40 |
3.5 |
- |
Keeping
Pressure 2 |
70-80 |
25-35 |
3.0 |
- |
Keeping
Pressure 3 |
70-75 |
20-30 |
2.5 |
- |
Temperature
setting
|
Setting
Temperature  |
Actual
Temperature  |
I |
60±5 |
60±5 |
II |
80±5 |
80±5 |
III(Stabling
Moulding) |
135-155 |
135-155 |
IV(stiring
Moulding) |
155-170 |
155-170 |
Innitialization
of open/close moulding
|
Pressure
(MPa) |
Speed |
Terminal
Position |
Mould
open speed |
30 |
60 |
100 |
Mould
open low Temperature |
10 |
10 |
|
Mould
open high temperature |
110 |
25 |
|
Mould
open slowly I |
60 |
20 |
25-45 |
Mould
open quickly |
45 |
50 |
250 |
Mould
open slowly II |
20 |
10 |
|
Mould
support setting
|
Pressure
(MPa) |
Speed |
Terminal
Position |
Moulding
enter |
50 |
45 |
According
to product's thickness |
Moulding
exit |
50 |
40 |
Mould
support method |
According
to different requirement of products, usually
holding is
preferred. |
Notes:
The above indexes are based on standard
environment, can be adjusted according cording
to different injection material models or actual
condition. |